Welcome to an informative article on equipment corrosion prevention in coal mining operations. As...
Chemicals Maintenance in Mining
In this article, we will discuss a very important topic which is chemical maintenance solutions in the coal mining industry.
Welcome to the complex and challenging world of coal mining. As one of the largest industrial sectors in Indonesia, coal mining plays a crucial role in our country's economy. However, with the sheer scale of operations and complexity of the processes involved come a variety of challenges that must be overcome to ensure the efficiency, safety and sustainability of mining operations.
Coal mining is not an easy job. Every day, miners face a variety of risks and challenges, ranging from extreme environmental conditions to potential hazards associated with heavy equipment and chemicals. One critical aspect that often receives less attention is the important role chemical maintenance plays in maintaining smooth mine operations.
Imagine a large coal mine in the interior of Borneo. Every day, thousands of tons of coal are hauled from the earth, processed and shipped to various parts of the world. Behind this massive operation, there is a complex system involving various equipment, machinery and chemical processes that must run flawlessly. From wastewater management to corrosion prevention on vital equipment, chemical maintenance solutions play an irreplaceable role.
But why is chemical maintenance so important? The answer is simple yet profound: without proper chemical management, mining operations can face a variety of serious problems. Imagine if a mine's wastewater treatment system is not functioning properly. The results could be devastating, not only to the surrounding environment but also to the reputation and operating license of the mining company itself.
On the other hand, implementing the right chemical maintenance solution can provide many benefits. From increased operational efficiency, reduced equipment downtime, to meeting increasingly stringent environmental standards. All of this ultimately contributes to the profitability and long-term sustainability of mining operations.
In this article, we will look at how to implement the right chemical maintenance solution.
In this article, we will explore various aspects of chemical maintenance solutions in the context of coal mining in Indonesia. We will discuss the common challenges faced by the industry, the innovative solutions available, as well as the importance of choosing the right partner in implementing these solutions.
As a country with vast coal reserves, Indonesia's coal mining industry has a lot to offer.
As a country with abundant coal reserves, Indonesia has a unique position in the industry. However, with this natural wealth also comes a great responsibility to manage it responsibly and sustainably. This is why an in-depth understanding of chemical maintenance solutions is so important for all stakeholders in the coal mining industry in the country.
Let's start our journey with a look at the coal reserves in Indonesia.
Let's begin our journey by taking a closer look at the specific challenges faced by the coal mining industry in Indonesia in the context of chemical maintenance. From there, we will explore the various solutions available, the latest technologies, as well as best practices that can be applied to overcome these challenges.
Please note that this article is not meant to be an exhaustive list of solutions.
Keep in mind that this article is not just for chemists or mining engineers. Rather, we hope this information will be useful to a wide range of people, from students interested in the mining industry, to decision-makers in mining companies who want to understand more about the importance of the chemical maintenance aspect of their operations.
So, are you ready for this article?
So, are you ready to dig deeper into the world of chemical maintenance solutions in coal mining? Let's start our journey!
Key Challenges in Chemical Maintenance in Coal Mining
Before we discuss solutions, it is important to understand the key challenges that the coal mining industry faces in the context of chemical maintenance. Here are some of the most significant challenges:
1. Wastewater Management
One of the biggest challenges in coal mining is wastewater management. The coal mining and processing process generates huge volumes of wastewater, which often contains a variety of hazardous contaminants. These contaminants can include heavy metals, acids, and various organic substances that can damage the environment if not properly treated.
The main challenge is how to treat this wastewater effectively and efficiently. An inadequate wastewater treatment system can lead to environmental pollution, which in turn can result in legal sanctions and damage to a company's reputation. On the other hand, overly expensive or complex treatment systems can put a strain on a company's operations.
2. Dust Control
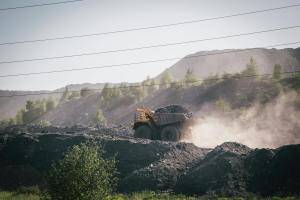
Dust is a big problem in coal mines. As well as being a health risk to workers, coal dust can also cause operational and environmental problems. Flying dust can impair visibility, damage equipment, and pollute the air around the mine area.
A key challenge is how to effectively control dust without disrupting mine operations or using too much water, which can be a scarce resource at some mine sites.
3. pH control
Coal mining often produces acid mine drainage which can be very damaging to the environment if not managed properly. This acid water is formed when sulfide minerals in coal are exposed to air and water, producing sulfuric acid.
The challenge is how to control the pH.
The challenge is how to effectively control the pH of this water. Too acidic, and the water can damage ecosystems and infrastructure. Too alkaline, and it can cause other problems such as heavy metal deposition.
4. Compliance with Environmental Regulations
Environmental regulations for the mining industry have gotten stricter over time. Mining companies are required to meet increasingly higher standards in terms of waste management, emissions, and overall environmental impact.
The challenge is how to meet or exceed them.
The challenge is how to meet or even exceed these standards without compromising operational efficiency or profitability.
5. Chemical Management
Coal mining operations use a large variety of chemicals. These range from chemicals for water treatment to reagents for coal refining. The management of these materials requires special attention.
Challenges include safe storage, proper handling, and responsible disposal. Errors in chemical management can lead to serious accidents, environmental pollution, or waste of resources.
6. Water Resources Management
Water is a critical resource in coal mining operations. However, in many mine sites, clean water can be a scarce resource.
The challenge is how to optimize water use, increase water recycling, and reduce overall water consumption without disrupting mine operations.
7. Technology Innovation and Adaptation
Technology in the field of chemical maintenance is constantly evolving. However, adopting new technologies is not without its challenges.
Challenges include high initial investment costs, training needs for staff, and risks associated with implementing untested technologies on a large scale.
All of these challenges are interconnected.
All of these challenges are interrelated and require a holistic approach to overcome. In the next section, we will discuss various solutions and approaches that can be used to address these challenges.
Innovative Solutions for Chemical Maintenance in Coal Mining
After understanding the key challenges, let's explore some innovative solutions that can be implemented to address these issues. It is important to note that there is no "one-size-fits-all" solution; each mine has unique characteristics that require a customized approach.
1. Advanced Wastewater Treatment System
To address wastewater management challenges, the coal mining industry is now turning to more advanced water treatment systems. One technology that is gaining popularity is the use of ultrafiltration and reverse osmosis membranes.
Ultrafiltration systems.
Ultrafiltration systems, such as those offered by Asahi Ultrafiltration Membranes, can effectively remove suspended particles, bacteria, and even viruses from mine wastewater. This technology allows for more efficient wastewater treatment and produces treated water that can be reused in mine operations, reducing overall clean water requirements.
For cases that require a higher level of purification, reverse osmosis systems can be used. This technology is capable of removing almost all contaminants, including dissolved salts and heavy metals, resulting in highly purified water.
2. Environmentally Friendly Dust Control Technology
To address dust issues, the coal mining industry is now adopting a more environmentally friendly approach. One solution that is gaining popularity is the use of bio-based dust suppressants that are safe for the environment.
Products such as Terragard Dust Control Chemicals can effectively control dust without the use of large amounts of water or harmful chemicals. These products work by binding dust particles together, preventing them from flying into the air.
In addition, the use of a dust control system is a great way to control dust.
In addition, the use of automated spraying systems and mining techniques that minimize dust production are also increasingly common.
3. Real-time pH Monitoring System
To address the challenges of pH control, especially in the context of acid mine drainage, the industry is now adopting real-time pH monitoring systems. These systems, often integrated with IoT (Internet of Things) solutions, enable continuous monitoring and control of pH.
By using pH sensors connected to a central control system, mine operators can immediately detect changes in pH and take corrective action before problems become serious. This not only increases the effectiveness of pH control but also reduces the risk of uncontrolled release of acidic water into the environment.
4. Integrated Environmental Management System
To meet increasingly stringent environmental regulations, many mining companies are now adopting an integrated Environmental Management System (EMS). These systems cover all aspects of mining operations, from wastewater management to emissions control.
An effective EMS not only helps companies meet regulatory standards, but can also improve overall operational efficiency. For example, by monitoring and optimizing chemical usage, companies can reduce costs while minimizing environmental impact.
5. Digital Chemical Management System
To improve efficiency and safety in chemical management, many mines are now adopting digital chemical management systems. These systems allow real-time tracking of chemical inventory, usage, and disposal.
6. Advanced Water Recycling Technology
To address the challenges of water resource management, many mines are now adopting advanced water recycling technologies. This includes the use of multi-stage treatment systems that allow wastewater to be treated to a quality that meets standards for reuse in various mine processes.
Systems such as Betaqua Ultrafiltration and Betaqua Reverse Osmosis can be used in combination to produce high-quality water from various mine wastewater sources.
Effective Implementation of Chemical Treatment Solutions
After understanding the various innovative solutions available, the next step is how to effectively implement these solutions. Proper implementation involves not only selecting the appropriate technology, but also ensuring that the solution is well integrated into the overall mine operation.
1. Comprehensive Assessment
The first step in effective implementation is to conduct a thorough assessment of the mine operation. This involves a detailed analysis of all aspects of the operation relating to chemical maintenance, including:
- Wastewater characteristics and specific treatment challenges
- Current chemical usage patterns
- Condition of existing equipment and infrastructure
- Compliance with environmental regulations
- Energy efficiency and water usage
This assessment will help identify priority areas for improvement and ensure that the solution selected is truly suited to the specific needs of the mine.
2. Selection of the Right Technology
Based on the results of the assessment, the next step is to select the most suitable technology. This is not just about choosing the latest or most advanced technology, but the most suitable for the specific conditions of the mine. Some factors to consider include:
- The effectiveness of the technology in addressing the specific challenges
- Initial investment costs and long-term operating costs
- Ease of integration with existing systems
- Availability of technical support and spare parts
- Potential for future scalability
For example, for wastewater treatment, a system such as Betaqua Ultrafiltration may be the right choice due to its effectiveness in removing various contaminants and its ability to be integrated with other treatment systems.
3. Careful Implementation Planning
Once a technology has been selected, the next step is to carefully plan for implementation. This involves:
- Preparing a realistic implementation schedule
- Identification and mitigation of potential risks
- Planning to minimize disruption to ongoing operations
- Coordination with various departments and stakeholders
It is important to involve all relevant parties in this planning process, including operational teams, maintenance teams, and environmental compliance teams.
4. Training and Capacity Building
The implementation of new technologies often requires new skills. Staff training and capacity building is therefore a critical component of successful implementation. This involves:
- Technical training for operators and maintenance teams
- Safety training for handling new chemicals
- Development of new or updated standard operating procedures (SOPs)
- Mentoring program to ensure effective knowledge transfer
Investment in training not only improves implementation effectiveness but also contributes to long-term operational safety and efficiency.
5. Continuous Monitoring and Evaluation
Implementation is not a one-off process. It is important to conduct continuous monitoring and evaluation to ensure that the implemented solution delivers the expected results. This involves:
- Regular collection and analysis of performance data
- Comparison of actual results with set targets
- Identification of areas for further improvement
- Adjustment and optimization based on feedback and operational data
Automated monitoring systems such as Betaqua Sentinel WS for Water Treatment System Monitoring can greatly assist in this process, providing real-time data that can be used for quick and informed decision making.
6. Partnership with the Right Solution Provider
Choosing the right partner in the implementation of chemical maintenance solutions is key to success. The ideal partner not only provides the technology, but also provides comprehensive support, including:
- Technical consultation in solution selection and implementation
- Support in training and capacity building
- After-sales service and continuous technical support
- Flexibility in customizing solutions to specific needs
A company like PT Beta Pramesti, with over 39 years of experience in the water and wastewater treatment industry in Indonesia, can be a valuable partner in this process. With the ability to design, build, and maintain complex water treatment systems, as well as manufacture specialty chemicals such as PAC and ACH, they can provide comprehensive solutions tailored to the specific needs of the coal mining industry in Indonesia.
Implementation of effective maintenance solutions in Indonesia is a key part of this process.
Effective implementation of chemical maintenance solutions is no easy task, but with the right approach and a reliable partner, coal mining companies can significantly improve their operational efficiency, reduce environmental impact, and ensure compliance with increasingly stringent regulations.
In this concluding section, we will look at the most important aspects of chemical maintenance in Indonesia.
In the concluding section, we will summarize the key points and look to the future of the coal mining industry in the context of chemical maintenance.
Conclusion: The Future of Chemical Maintenance in Coal Mining
After exploring the various aspects of chemical maintenance solutions in coal mining, let's summarize the key points and look to the future of the industry.
First of all, it is clear that chemical maintenance is not an aspect that can be overlooked in coal mining operations. From wastewater management to corrosion prevention, from dust control to coal refining, chemistry plays a crucial role at every stage of a mine operation. Neglecting this aspect not only risks operational efficiency, but can also result in serious environmental impacts and regulatory compliance.
Secondly, we have seen that