The oil and gas industry is an important sector in the global economy, with water being a crucial...
Use of Chemical Degreasers to Clean Oil and Grease on Heavy Equipment
Coal mining is a very important industry for Indonesia. As one of the world's largest coal producers, our country has a great responsibility to ensure that mining practices are carried out in an efficient and environmentally friendly manner. One of the major challenges in coal mining operations is the handling of oil and grease generated from various equipment and processes. Effective oil and grease removal is not only important to maintain equipment performance, but also to protect the environment from potential pollution.
In this article, we will discuss the use of Degreaser Chemical for oil and grease removal in the coal mining industry. We will explore various aspects ranging from the main sources of oil and grease in mining operations, the negative impacts that can be caused if not handled properly, to the latest techniques in the use of degreasers to address these issues.
As a country with rich resources of oil and grease, the coal mining industry has a lot to offer.
As a country with abundant natural resources, Indonesia has many coal mines spread across various regions, especially on the islands of Kalimantan and Sumatra. Every year, millions of tons of coal are produced from these mines, contributing significantly to the national economy. However, as production increases, environmental challenges also become more complex. One aspect that often receives less attention is the management of oil and grease generated from mining operations.
Oil and grease in mining is an important part of the environment.
Oil and grease in coal mining comes from various sources. Heavy equipment such as excavators, bulldozers and haul trucks use large amounts of lubricating oil to maintain their smooth operation. In addition, the hydraulic systems used in various mining equipment also contain oil. Routine maintenance and equipment repairs often result in oil spills or leaks that must be cleaned up. Even the process of washing equipment can produce waste water contaminated with oil.
If not handled properly, this accumulation of oil and grease can cause a variety of problems. First, from an operational perspective, oil and grease buildup can reduce equipment efficiency, accelerate wear and tear, and even cause breakdowns. This in turn increases maintenance costs and reduces mine productivity. Secondly, from a safety perspective, slippery surfaces caused by oil spills can increase the risk of accidents. Third, and perhaps most important, is the environmental impact. Oil and grease contaminating the soil or water can damage local ecosystems, contaminate water sources, and even jeopardize the health of communities around the mining area.
Considering the magnitude of these challenges, it is important to recognize that there are many ways to deal with them.
Given the magnitude of these challenges, the coal mining industry in Indonesia needs to adopt best practices in oil and grease management. One effective solution is the use of degreasers or oil cleaners. Degreasers are specialized chemicals designed to break down and remove oil and grease from various surfaces. In the context of coal mining, degreasers have an important role to play in cleaning equipment, work areas, and even in the treatment of oil-contaminated wastewater.
However, the use of degreasers in coal mining can be very costly.
However, the use of degreasers is not a simple solution. There are different types of degreasers with different characteristics and applications. Proper selection and use of degreasers requires an in-depth understanding of their chemical properties, effectiveness, environmental impact, as well as safe usage procedures. In addition, the integration of degreaser use into a broader environmental management system is also an important aspect that needs to be considered.
In this article, we will explore in detail the various aspects of degreaser use in the context of coal mining in Indonesia. We will discuss the types of degreasers available, appropriate selection criteria, effective application techniques, as well as best practices in degreasing waste management. In addition, we will also look at how the latest technologies and innovations in this field can help improve efficiency and reduce environmental impact.
As an important note, while this article focuses on the use of degreasers, keep in mind that a holistic approach to oil and grease management is essential. This includes spill prevention efforts, preventive maintenance of equipment, as well as the implementation of a comprehensive environmental management system. By understanding and implementing best practices in oil and grease removal, the coal mining industry in Indonesia can improve operational efficiency, maintain worker safety, and most importantly, protect the environment for future generations.
Main Sources of Oil and Grease in Coal Mining
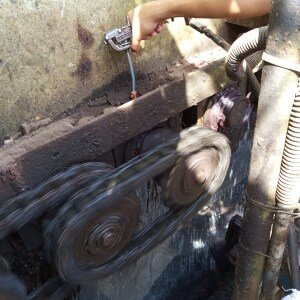
Before we discuss more about degreaser usage, it is important to understand the major sources of oil and grease in coal mining operations. This understanding will help us identify critical areas that require special attention in oil and grease management.
1. Heavy Equipment: Tools such as excavators, bulldozers, and haul trucks use large amounts of lubricating oil. Small leaks from worn seals or joints can accumulate significant oil over time.
2. Hydraulic Systems: Many mining equipment uses hydraulic systems that contain high-pressure oil. Leaks in these systems can lead to sizable oil spills.
3. Maintenance Areas: Equipment maintenance shops and areas are often the point of oil and grease accumulation due to repair and component replacement activities.
4. Refueling Stations: Small spills during refueling can accumulate over time, creating an oil-contaminated area.
5. Conveyor Belts: Conveyor systems used for coal transportation often require lubrication, which can lead to the accumulation of oil around the area of operation.
6. Equipment Washing Areas: The process of cleaning mining equipment can generate wastewater contaminated with oil and grease.
7. Oil and Fuel Storage Areas: These storage areas are at risk of leaks or spills that could contaminate the surrounding environment.
Understanding these sources is important for designing an oil and fuel management strategy.
Understanding these sources is important for designing an effective oil and grease management strategy. Each area has unique characteristics and challenges that require a specific approach in the use of degreasers and other cleaning techniques.
Negative Impacts of Oil and Grease Accumulation
Oil and grease accumulation in coal mining operations can have a variety of significant negative impacts. Understanding these impacts is important to realize the urgency of effective management.
1. Environmental Impacts:
- Soil Pollution: Oil and grease leaching into the soil can damage soil structure and inhibit plant growth.
- Water Pollution: Contamination of water sources by oil can damage aquatic ecosystems and jeopardize the health of people who depend on these water sources.
- Impact on Fauna: Animals exposed to oil and grease can experience various health problems.
2. Safety Risks:
- Slippery Surfaces: Oil accumulation in work areas can make surfaces slippery, increasing the risk of slips and falls.
- Fire Risk: Accumulated oil and grease can increase the risk of fire, especially in areas with heat sources or sparks.
3. Operational Issues:
- Equipment Damage: Excessive oil and grease can accelerate component wear and cause premature damage to equipment.
- Decreased Efficiency: Equipment contaminated with oil and grease tends to run less efficiently, increasing fuel consumption and lowering productivity.
4. Legal and Financial Implications:
- Regulatory Violations: Failure to properly manage oil and grease can lead to violations of environmental regulations, potentially resulting in fines and penalties.
Restoration Costs: The cost of cleaning up oil spills and restoring contaminated areas can be very high.
5. Corporate Image:
- Negative Reputation: Poor oil and grease management can damage a company's reputation, especially in the eyes of the community and other stakeholders.
Given the magnitude of these negative impacts, effective oil and grease management is critical. The proper use of degreasers is one of the key components in a comprehensive management strategy.
Types of Degreasers and Their Selection
Degreasers come in many different types, each with different characteristics and applications. Proper degreaser selection is critical to ensure cleaning effectiveness while minimizing environmental impact. Here are some of the main types of degreasers commonly used in the coal mining industry:
1. Solvent Based Degreasers:
- Characteristics: Very effective for heavy oils and greases, but generally more harmful to the environment.
- Examples: Petroleum-based or chlorinated degreasers.
- Uses: Suitable for intensive cleaning of heavy equipment, but requires special handling and disposal.
2. Water-Based Degreasers:
- Characteristics: More environmentally friendly, safe for most surfaces, but may be less effective for heavy contamination.
- Examples: Alkaline or neutral degreasers.
- Uses: Ideal for routine cleaning and areas with light to moderate contamination.
3. Biodegradable Degreasers:
- Characteristics: Made from natural or synthetic materials that degrade easily, environmentally friendly.
- Example: Citrus or enzyme based degreasers.
- Usage: Suitable for environmentally sensitive areas or where disposal is an issue.
4. Emulsion Degreasers:
- Characteristics: Combines the properties of solvents and water, effective for different types of contaminants.
- Example: Semi-aqueous emulsion degreaser.
- Usage: Versatile, suitable for various applications in mining.
5.
5. Foaming Degreasers:
- Characteristics: Forms a foam that sticks to vertical surfaces, increasing contact time.
- Example: Foaming alkaline degreaser.
- Usage: Effective for cleaning large equipment or vertical surfaces.
In choosing the right degreaser, some factors to consider include:
1. Type and Level of Contamination: Adjust the strength of the degreaser to the level and type of oil or grease to be cleaned.
2. Material Compatibility: Ensure that the degreaser does not damage the surface or component being cleaned.
3. Application Method: Consider how the degreaser will be applied (spray, soak, brush, etc.).
4. Environmental Considerations: Choose products that have minimal impact on the environment, especially if used in sensitive areas.
5. Regulations and Compliance: Ensure that the degreaser selected meets applicable environmental and safety regulatory standards.
6. Cost Efficiency: Consider not only the price of the product, but also the effectiveness, quantity required, and disposal costs.
7. Worker Safety: Choose products with low levels of toxicity and volatility to maintain worker safety.
A good example of an effective and environmentally friendly degreaser is an effective and environmentally friendly degreaser.
One example of an effective and environmentally friendly degreaser is the Terragard Degreaser product developed specifically for the mining industry. This product is designed to tackle heavy oil and grease contamination while keeping safety and environmental aspects in mind.
It is important to remember that there is no such thing as an effective degreaser.
It is important to remember that no one type of degreaser is suitable for all situations. Often, a combination of several types of degreasers may be required to address various cleaning challenges in coal mining operations. Consultation with an industrial chemist or professional cleaning solutions provider can assist in selecting the degreaser best suited for the specific needs of your mining operation.
Effective Degreaser Application Techniques
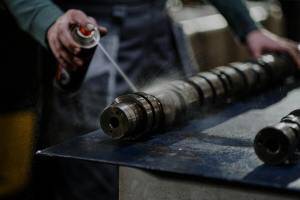
After choosing the right degreaser, the next step is to apply it in an effective manner. Correct application techniques not only improve cleaning efficiency but also help optimize product usage and minimize environmental impact. Here are some effective degreaser application techniques in the context of coal mining:
1. Pre-cleaning:
- Clear the area of dirt and large debris before applying the degreaser.
- Use high-pressure water or compressed air to remove dust and loose particles.
2. Degreaser Application:
- For small areas: Use a spray bottle or brush to apply degreaser evenly.
- For large areas: Use a low- or high-pressure spray system, depending on the type of degreaser and the level of contamination.
- For large equipment: Consider using a fog or mist system to reach hard-to-reach areas.
3. Contact Time:
- Allow the degreaser to work for the time recommended by the manufacturer.
- For heavy contamination, longer contact times or repeated applications may be required.
4. Agitation:
- Use a brush or pad to agitate the degreaser on heavily soiled surfaces.
- For large areas, consider using an automatic scrubber machine.
5. Rinsing:
- Rinse the cleaned area with clean water, ideally using high-pressure water.
- Ensure all degreaser residue is removed to prevent further corrosion or contamination issues.
6. Drying:
- Allow the area to dry naturally or use compressed air to speed up the drying process.
- For sensitive equipment, consider using a clean cloth or air dry to remove any residual moisture.
7. Special Techniques for Specific Areas:
- For hydraulic systems: Use a flushing method with a specialized degreaser compatible with hydraulic systems.
- For conveyor belts: Apply the degreaser while the belt is moving slowly to ensure even coverage.
8. Use of Auxiliary Tools:
- For hard-to-reach areas, use an extension nozzle or other specialized equipment.
- Consider using an automated cleaning system for routine cleaning tasks on large equipment.
9. Waste Handling:
- Collect cleaned wastewater for treatment before disposal.
- Use an oil-water separation system such as Dissolved Air Flotation (DAF) to separate oil from wastewater.
10. Monitoring and Documentation:
- Perform a visual inspection after cleaning to ensure effectiveness.
- Document the cleaning process, including the type of degreaser used, application method, and results achieved.
- Document the cleaning process.
It is important to remember that safety should always be a top priority when applying degreasers. Ensure all workers involved in the cleaning process are equipped with the appropriate personal protective equipment (PPE), including gloves, goggles, and masks if required. Also, ensure the work area is adequately ventilated, especially when using solvent-based degreasers.
To improve efficiency and consistency in the cleaning process, consider developing detailed standard operating procedures (SOPs) for different types of cleaning tasks. These SOPs should include the specific steps, the type of degreaser used, the contact time required, and the safety procedures that must be followed.
Finally, don't forget to keep in mind that you can't use a solvent-based degreaser.
Finally, don't forget to regularly evaluate the effectiveness of your cleaning process. This may include conducting wastewater quality testing, periodic equipment inspections, and collecting feedback from operators. This information can help you continue to refine your degreaser application techniques and ensure that your cleaning practices remain effective and efficient as time goes on.
Waste Management of Degreasing Process Results
Management of the waste generated from the degreasing process is a critical aspect of responsible oil and grease removal practices. This waste, which is generally a mixture of water, degreaser, and oil contaminants, requires special handling to prevent negative impacts on the environment. Here are some best practices in the management of degreasing process waste:
1. Oil-Water Separation:
- Use an oil-water separation system such as Dissolved Air Flotation (DAF) to separate oil from wastewater.
- This technology is effective in removing oil and suspended particles from wastewater.
2. Advanced Treatment:
- After initial separation, wastewater may require advanced treatment.
- Consider the use of ultrafiltration or reverse osmosis systems to remove remaining contaminants.
3. Water Recycling:
- Where possible, recycle treated water for reuse in cleaning processes or other operations.
- This can reduce fresh water consumption and minimize waste discharges.
4. Management of Recovered Oil:
- Oil that is successfully separated can be recycled or reused if possible.
- If it cannot be reused, ensure disposal is through an authorized hazardous waste treatment facility.
5. Use of Bioremediation:
- For soil contamination by oil, consider the use of bioremediation techniques.
- Products such asBetagard's bacteria and enzymes can help degrade oil contaminants naturally.
6. Water Quality Monitoring:
- Perform regular testing on treated wastewater to ensure compliance with environmental standards.
- Use an automated monitoring system such as Sentinel WS for real-time monitoring of water quality.
7. Documentation and Reporting:
- Record all effluent management activities, including volumes treated, treatment methods, and test results.
- Retain this documentation for auditing and reporting purposes to environmental authorities.
8. Staff Training:
- Ensure that all personnel involved in waste management are properly trained on the correct procedures and the importance of responsible waste management.
9. Evaluation and Continuous Improvement:
- Periodically evaluate the effectiveness of your waste management system.
- Continually look for ways to improve efficiency and reduce environmental impact.
By implementing these practices, you will be able to improve your waste management system.
By implementing these practices, coal mining operations can significantly reduce the environmental impact of the degreasing process while ensuring compliance with applicable environmental regulations. Effective waste management not only protects the environment but can also result in cost savings through reduced water consumption and improved operational efficiency.
Latest Innovations and Technologies in Oil and Grease Removal
The coal mining industry is constantly evolving, and so are the technologies used in oil and grease removal. The latest innovations not only improve the efficiency of the cleaning process but also minimize the environmental impact. Here are some of the latest innovations and technologies worth noting:
1. Nano-technology degreasers:
- Uses nano-particles to improve penetration and cleaning effectiveness.
- Allows the use of fewer chemicals with better results.
2. Ultrasonic Cleaning System:
- Uses high frequency sound waves to clean equipment.
- Very effective for cleaning hard to reach areas on complex equipment.
3. Enzyme Based Degreaser:
- Uses natural enzymes to break down oil and grease molecules.
- Eco-friendly and biodegradable, ideal for environmentally sensitive areas
4. Automated Cleaning Systems:
- Programmable cleaning robots to automatically clean specific areas.
- Improves consistency and reduces worker exposure to hazardous chemicals.
5. Real-time Monitoring Technology:
- Advanced sensors that can detect the level of oil contamination in real-time.
- Enables rapid response to spills or leaks.
6. Integrated Wastewater Treatment System:
- Combination of technologies such as DAF, ultrafiltration, and reverse osmosis in one integrated system.
- Improves wastewater treatment efficiency and enables more effective water recycling.
7. Supercritical CO2 Based Degreaser:
- Uses CO2 under supercritical conditions as a solvent to clean oil and grease.
- Highly effective and environmentally friendly, with no harmful residue.
8. Advanced Bioremediation Technology:
- Use of genetically engineered microorganisms to degrade oil contaminants more quickly and efficiently.
- Ideal for the restoration of oil-contaminated land.
9. Smart Waste Management Systems:
- Uses IoT (Internet of Things) and AI to optimize the waste management process.
- Allows for better monitoring and control over the entire waste management cycle.
What are some of these technologies?
Although many of these technologies are still in the development stage or just beginning to be implemented, they offer great potential for improving oil and grease removal practices in the coal mining industry. Companies such as PT Beta Pramesti, with over 39 years of experience in the water and wastewater treatment industry, are at the forefront of adopting and developing these technologies for the Indonesian market.
It is important for mining companies to continuously improve their oil and grease removal practices.
It is important for mining companies to keep abreast of these technologies and consider their application according to the specific needs of their operations.