The coal mining industry is one of the most challenging sectors in terms of equipment maintenance....
Chemicals for Coal Mining Belt Conveyor Maintenance
The coal mining industry is one of the important sectors in the Indonesian economy.
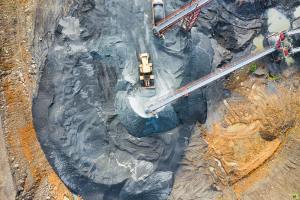
As the fifth largest coal producing country in the world, Indonesia has its own challenges in managing efficient and sustainable mining operations. One of the critical components in coal mining operations is the belt conveyor system, which plays an important role in the transportation of mined material from the excavation site to the processing or shipping area.
Belt Conveyors face various stresses and wear in their daily use. Exposure to coal dust, moisture, extreme temperatures, and heavy loads can accelerate damage to vital components of the conveyor system. Therefore, regular maintenance and the use of proper maintenance chemicals are of paramount importance to ensure optimum performance and prolong the life of the conveyor system.
In this article, we will be looking at the different types of conveyor belts.
In this article, we will take an in-depth look at the common maintenance chemicals used to treat belt conveyors in coal mining. We will explore the functions, benefits, and usage of different types of maintenance chemicals, as well as discuss the importance of proper product selection and effective maintenance practices.
The Importance of Belt Conveyor Maintenance
Before we dive into the types of maintenance chemicals, it is important to understand why belt conveyor maintenance is crucial in coal mining operations:
- Operational Efficiency: Well-maintained Belt Conveyors operate more efficiently, reducing downtime and increasing mine productivity.
- Safety.
- Safety: Proper maintenance reduces the risk of accidents due to equipment failure or fires caused by excessive friction.
- Safety.
- Cost Savings: While the initial investment for maintenance may seem high, it can save costs in the long run by avoiding major repairs or premature replacement of equipment.
- Cost Savings.
- Product Quality: A well-functioning belt conveyor helps maintain coal quality during the transportation process, reducing contamination and material damage.
- Product Quality.
- Environmental Compliance: Good maintenance can help reduce dust and noise emissions, helping mine operations comply with environmental regulations.
- Environmental Compliance.
Understanding the importance of these treatments, let's explore more about the commonly used treatment chemicals in the coal mining industry.
Types of Common Maintenance Chemicals
Belt Conveyor Lubricants
Lubricants are one of the most important maintenance chemicals for belt conveyors. Its main function is to reduce friction between the belt and other components, such as rollers and pulleys. A good lubricant can:
- Reduce wear on the belt and other components
- Lower energy consumption by reducing friction
- Helps prevent overheating that can cause fires
- Protects the belt from corrosion and oxidation
There are several types of lubricants commonly used, including mineral oil-based lubricants, synthetic lubricants, and dry lubricants. The choice of lubricant type depends on the specific operating conditions, such as ambient temperature, workload, and type of material being transported.
Use example: Apply lubricant regularly to critical points such as bearings and rollers. Use automated lubrication systems where possible to ensure consistent application and reduce the need for manual intervention.
Belt and Component Cleaner
Coal dust and other debris can build up on conveyor belts and components, reducing efficiency and potentially causing damage. Specialized cleaners are required for:
- Remove accumulated dust, oil, and dirt
- Preparing surfaces for lubricant or sealant application
- Prevent contamination of transported material
- Increases visibility for visual inspection
These cleaners are typically available in liquid or aerosol form and are often formulated to remove specific contaminants commonly encountered in coal mining environments.
These cleaners are typically available in liquid or aerosol form and are often formulated to remove specific contaminants commonly encountered in coal mining environments.
Example of use: Use the cleaner before performing routine inspections or prior to lubricant application. Ensure the cleaned area is fully dry before applying other maintenance chemicals.
Sealants and protectants
Sealants and protectants are used to protect Conveyor Belts and their components from damage due to exposure to aggressive elements such as moisture, corrosive chemicals, and abrasion. These products can:
- Form a protective film on the belt surface
- Prevent penetration of water and corrosive chemicals
- Increase abrasion resistance
- Helps extend belt and component life
Some commonly used sealant types include silicone, polyurethane, and epoxy-based sealants. The selection of sealant type depends on the type of belt material and operating conditions.
Example of use: Apply sealant to belt joints and areas prone to damage. Ensure surfaces are clean and dry before application. Allow sealant to dry completely per manufacturer's instructions before operating conveyor.
Anti-Static Chemicals
In coal mining environments, the accumulation of static electricity on Conveyor Belts can be a serious problem, potentially causing sparks and fires. Anti-static chemicals are used for:
- Reduce the accumulation of electrostatic charge on the belt
- Prevent sparks that can ignite coal dust
- Increase operational safety
Anti-static chemicals are usually applied as a spray or liquid that forms a conductive layer on the belt surface.
- .
Use case: Apply anti-static agents regularly, especially in dry seasons or in areas with low humidity. Ensure even coverage over the entire belt surface.
Corrosion Inhibitor
Metal components of conveyor systems, such as rollers, bearings, and support structures, are susceptible to corrosion, especially in environments that are humid or contain corrosive chemicals. Corrosion inhibitors serve to:
- Form a protective layer on the metal surface
- Inhibit the oxidation process that causes corrosion
- Extend the service life of metal components
- Reduce the frequency of component replacement
Corrosion inhibitors are available in various forms, including sprays, liquids, and pastes. Some products combine the function of a corrosion inhibitor with a lubricant for dual protection.
Use case: Apply corrosion inhibitors to exposed metal components, especially after cleaning or before long periods of inactivity. Pay attention to areas prone to water or condensate accumulation.
Rubber Treatment Chemicals
Conveyor belts are often made of rubber or rubber-based materials. Special treatment chemicals for rubber can help:
- Maintain rubber flexibility and elasticity
- Prevent drying and cracking
- Protect against degradation due to UV and ozone exposure
- Increases resistance to chemicals and oils
These products are usually in the form of a liquid or spray that is applied directly to the rubber surface.
- .
Example of use: Apply rubber treatment agents periodically, especially on parts of the belt that are directly exposed to sunlight or harsh environments. Avoid over-application which can make the belt surface too slippery.
Friction Reducing Additives
Friction reducing additives are used to reduce the friction between the conveyor belt and the material being transported, especially important in the transportation of coal which can be highly abrasive. Benefits of using these additives include:
- Reduces wear on belt surface
- Increases material transfer efficiency
- Reduces energy consumption
- Minimize dust generation during transportation
These additives are usually in the form of powders or liquids that are applied directly to the material or the belt.
Example of use: Apply friction-reducing additives at material transfer points or directly on coal piles before transportation. Adjust dosage based on material characteristics and operating conditions.
Choosing and Using the Right Treatment Chemical
Choosing the right treatment chemicals for Belt Conveyors in coal mining requires consideration of several factors:
- Material Compatibility: Ensure that the chemicals selected are compatible with the Belt Conveyor material and other components. Some chemicals may be able to damage certain rubbers or plastics.
- Environmental Conditions: Consider temperature, humidity, and exposure to other elements at the mine site. Chemicals must be able to withstand the existing operational conditions.
- Safety and Safety Regulations.
- Safety and Environmental Regulations: Select products that meet applicable safety and environmental standards. Be mindful of potential impacts to the environment and worker health.
- Effectiveness: Choose products that meet applicable safety and environmental standards.
- Effectiveness: Evaluate the product's performance in addressing the specific issues faced by your conveyor system.
- Effectiveness.
- Ease of Use: Consider the method of application and frequency of use required. Products that are easy to apply can save time and labor.
- Ease of Use.
- Cost: Consider not only the price of the product, but also the potential long-term savings from using a high-quality product.
- Cost.
After selecting the right chemical, it is important to follow good usage practices:
- Always read and follow the manufacturer's instructions for use.
- Use appropriate personal protective equipment (PPE) when handling chemicals.
- Store chemicals properly according to manufacturer's recommendations.
- Conduct small area testing first before large-scale application.
- Document chemical use and results for long-term effectiveness evaluation.
The Important Role of Suppliers and Technical Support
In the context of belt conveyor maintenance in coal mining, the role of chemical suppliers and the technical support they provide is critical. An experienced supplier not only provides products, but can also add value through:
- Technical consultation for proper product selection
- Training for maintenance staff on correct product usage
- On-site support to diagnose problems and optimize product usage
- Regular updates on product innovations and industry best practices
Choosing a local supplier with a good reputation can provide additional benefits such as faster product availability and a better understanding of the specific conditions in Indonesia. For example, PT Beta Pramesti offers a range of industrial chemical products including dust control chemicals that can be particularly beneficial in the context of coal mining.
Integration with Monitoring and Predictive Maintenance Systems
The use of treatment chemicals can be further optimized by integrating them into monitoring and predictive maintenance systems. Modern technology makes this possible:
- Real-time monitoring of conveyor belt condition
- Data analysis to predict maintenance needs
- Automatic scheduling for treatment chemical application
- Optimized chemical usage based on actual conditions
Systems such as PT Beta Pramesti's Sentinel WS for water treatment system monitoring can be adapted to monitor a wide range of conveyor system operational parameters, aiding in more informed maintenance decision making.
Conclusion
The use of appropriate maintenance chemicals is a critical component in ensuring optimal performance and long service life of Belt Conveyor systems in coal mining. From lubricants and cleaners to sealants and corrosion inhibitors, each type of chemical plays an important role in protecting equipment investments and ensuring efficient and safe operations.
However, it is important to keep in mind that there are many different types of maintenance chemicals available.
However, it is important to remember that the use of maintenance chemicals is only one aspect of a comprehensive maintenance strategy. Integration with other maintenance practices, such as regular inspections, mechanical adjustments, and operator training, is key to maximizing the benefits of using these chemicals.
In addition, given the importance of sustainability and environmental compliance in the modern mining industry, the selection of treatment chemicals should also consider environmental impact. Products that are more environmentally friendly and biodegradable are increasingly available and should be considered as part of the industry's commitment to more sustainable mining practices.
Finally, close collaboration and close collaboration are key to maximizing the benefits of using these chemicals.
Finally, close collaboration with experienced suppliers and utilization of advanced monitoring technologies can help coal mining operations in Indonesia to optimize the use of treatment chemicals, improve operational efficiency, and ultimately, increase competitiveness in an increasingly competitive global market.
Questions and Answers
Q1: How to choose the right lubricant for Belt Conveyors in dusty coal mining environment?
A1: Selecting the right lubricant for Belt Conveyors in dusty environments such as coal mining requires consideration of several factors. First, select a lubricant with a viscosity that is appropriate for the operating conditions. High viscosity lubricants tend to be more resistant to dust contamination. Second, consider lubricants with anti-wear and extreme pressure additives to protect components from wear due to abrasive particles. Thirdly, choose lubricants that have water-resistant properties to prevent corrosion. Finally, consider using PTFE or molybdenum disulfide-based dry lubricants that attract less dust than oil-based lubricants.
Q2: Can the use of anti-static chemicals replace the grounding system on a belt conveyor?
A2: Anti-static chemicals cannot completely replace a proper grounding system on a Belt Conveyor. Although anti-static chemicals are effective in reducing the accumulation of electrostatic charges on belt surfaces, they should be considered as an additional measure, not a replacement. A good grounding system is still required to ensure safe and effective dissipation of electrical charges. The combination of a proper grounding system and the use of anti-static chemicals provides a more comprehensive approach to managing electrostatic risk in coal mining environments.
Q3: How often should maintenance chemicals be applied to Conveyor Belts in coal mining?
A3.
A3: The frequency of application of maintenance chemicals on Belt Conveyors depends on several factors, including operating conditions, chemical type, and manufacturer's recommendations. In general, lubricants may need to be applied every week or two, while sealants and protectants may last longer, requiring application every few months. Anti-static materials may need to be applied more frequently, especially in dry conditions. It is important to conduct regular monitoring and adjust application schedules based on actual performance and environmental conditions. Consult with the chemical supplier and maintenance team to develop an optimal schedule for your specific operation.
References
- Smith, J.A. (2019). "Conveyor Belt Maintenance in Coal Mining Operations", Journal of Mining Engineering, Vol. 45, No. 3, pp. 78-92.
- Johnson, R.B. (2020). "Chemical Solutions for Dust Control in Mining Environments", Environmental Science & Technology, Vol. 54, Issue 12, pp. 7245-7259.
- Patel, S.K. and Mishra, A.K. (2018). "Advancements in Conveyor Belt Lubricants for Heavy-Duty Applications", Tribology International, Vol. 128, pp. 302-312.
- Australian Coal Association Research Program (ACARP) (2017). "Best Practice Maintenance Strategies for Coal Handling Conveyors", Report C25032. .
- World Coal Association (2021). "Sustainable Coal Mining Practices: A Global Perspective", Chapter 7: Equipment Maintenance and Efficiency, pp. 156-178. .